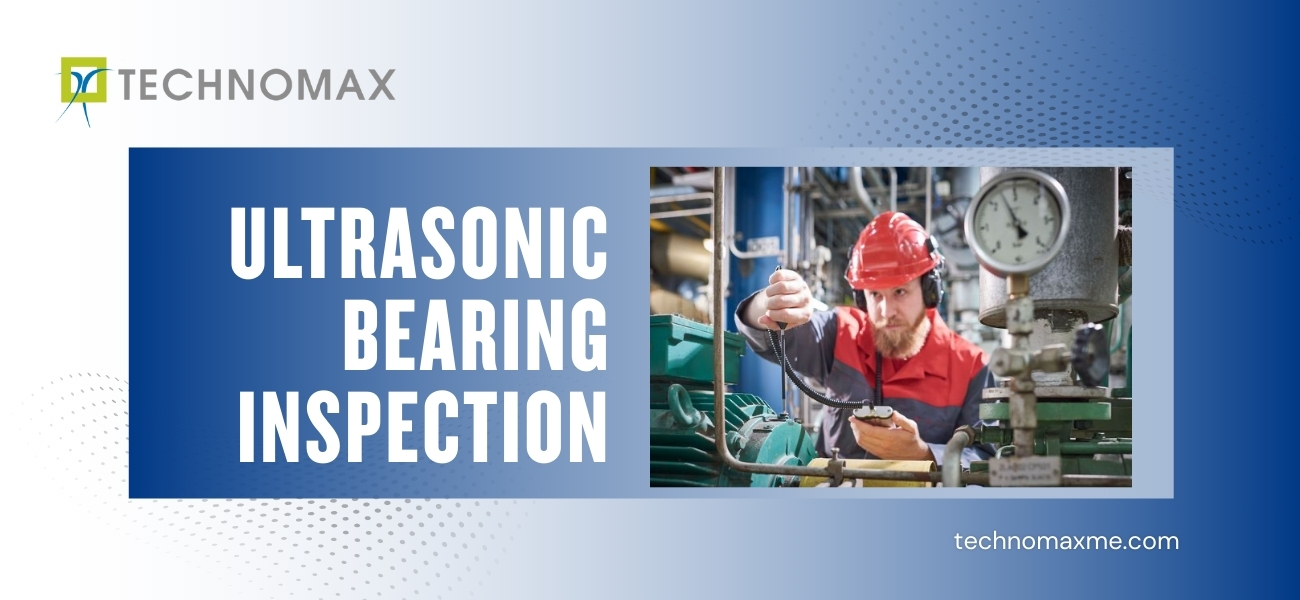
Bearing Inspection With Ultrasonic Devices
“Bearing Inspection” is basically checking the condition or state of bearings within equipment to determine if they are functioning properly and delivering the expected performance level. Bearings are vital in supporting the rotating shafts and minimising the friction between moving components. But they are susceptible to wear, damage, and misalignment.
Common causes of bearing issues include contamination, inadequate lubrication or excess load. When bearings fail, they can lead to equipment failure, unexpected costs and considerable downtime.
Temperature variations, visual checks or vibrations were mostly used metrics to analyse and assess the bearing condition conventionally, resulting in less precision; they often missed the faults and were detected only at an end stage when the anomalies had escalated. With the changing demands, grew the need for more advanced and accurate technology to inspect the bearing condition.
Here is where Ultrasonic bearing Inspection comes in—providing a non-invasive, more concise and advanced way to understand and evaluate the condition of your machinery bearings and detect faults, if any, early before they become significant. So, taking care of your bearings with regular checkups and maintenance goes a long way. It helps them function better and last longer. Plus, finding faults beforehand means fewer unexpected breakdowns or operational hindrances, and smoother equipment running.
This blog will explore an in-depth understanding of bearing inspection, focusing on its importance, benefits, techniques, leading ultrasonic devices and services.
Bearing Inspection: An Overview
The health of a bearing plays a great role in determining the overall reliability of your equipment. Relying upon guesswork to detect bearing issues is risky and can put your entire machinery in jeopardy. That’s why regular, detailed inspection is non-negotiable. It may not just reveal the exact condition of the bearing, but also ensure the asset's optimal performance without unexpected interruptions. Let us take a closer look at the key stages involved in bearing inspections:
- Initial Inspection: Before cleaning the bearings, the initial state and appearance of the bearings are recorded. The quantity and condition of residual lubricant will be noted. Following this, the lubricant is taken to assess the existing condition of the bearing.
- Bearing Cleaning: At this stage, bearings should be thoroughly cleaned to remove any contaminants, grease, dirt or debris that could conceal underlying wear or damage. Typically, the dismounted bearings undergo an initial cleaning followed by a finishing rinse, during which a light oil may be used as a cleaning agent. Removing the debris will enhance visibility of the bearing surfaces, providing a clearer view for evaluation.
- Inspection and Evaluation of Bearings: Once clean, bearings are checked for any signs of damage, scoring, pitting, deformation, etc. This is done through visual checks or inspecting the raceways, intensity of cage wear, distortion, measuring clearances and in advanced cases, using ultrasonic tools to find subsurface flaws. This will determine if the bearings are still fit to reuse, need conditioning or be replaced.
What is Ultrasonic Bearing Condition Monitoring?
Ultrasonic Bearing Condition Monitoring, or simply ultrasonic testing, is an effective way to identify bearing wear or damage faster. A great advantage of this method is its ability to spot the earliest signs of bearing failure. Ultrasonic testing is versatile enough to monitor high and low-speed bearings, even those operating at speeds as low as 1 RPM. This technique aids in both proactive and preventive maintenance.
When used at regular intervals to check and inspect for early signs of damage, clearly before a failure occurs, it can be a part of the scheduled preventive maintenance routine, helping to avoid unexpected breakdowns. As it detects concerns at the initial phase, before vibration or temperature variations occur, it allows addressing the underlying root causes, such as inadequate lubrication or misalignment. This facilitates taking corrective action proactively, which greatly extends the operational life of the bearing.
Benefits of Regular Ultrasonic Bearing Inspection
Ultrasonic testing is vital in modern maintenance practices as it enables early detection of faults in bearings. The testing devices are designed to detect high-frequency sound waves, often ranging from 20 kHz to 100 kHz, that are generated due to friction, impact, or a flaw within the bearing. Even the slightest pitting, scoring, lack of lubrication or fatigue cracks could be traced through ultrasonic testing before they advance to major issues.
Regular ultrasonic inspections are necessary for an effective preventive maintenance strategy in Industrial settings, where bearings are constantly exposed to varying loads, speeds and harsh conditions. The damage of a bearing alone in critical machinery like motors, pumps, gearboxes, etc, can bring the entire operation to a halt, which causes unplanned shutdowns, incurring huge losses, especially in industries where time is tied to production and revenue. Here are some of the major benefits:
- Early Detection of Bearing Faults: Ultrasonic testing or ultrasonic condition monitoring of the bearing helps identify the bearing issues early, before the problems become critical.
- Reduced Unplanned Downtime: Detecting the faults early gives the upper hand to plan maintenance rather than reacting to costly breakdowns and operational interruptions.
- Improved Precision and Real-time Diagnosis: Ultrasonic devices and tools provide instant readings and the most accurate fault detection data from hard-to-reach or enclosed bearing housings.
- Supports Predictive Maintenance: Ultrasonic testing enables data-driven decision making. Tracing the faults early aids in developing preventive strategies, extending the asset’s life and adding value in the long run.
- Saving on Repairs and Replacements: Through proper corrective and preventive actions, major damages and accidents can be averted, avoiding the need for repairs or replacements of components or machine parts.
- Improved efficiency and sustainability: By detecting faults beforehand, there will be fewer breakdowns and less energy and resources wasted, improving plant efficiency and contributing to sustainability.
Bearing Inspection with Sonotec’s Ultrasonic Devices
The major cause of the damaged bearing is inadequate lubrication, which increases the friction in the bearing, where acoustic emissions increase. Insufficient lubrication or over-usage can be quickly identified with advanced ultrasonic devices from Sonotec, such as the SONAPHONE and SONAPHONE POCKET.
Improper handling, foreign particles, and excessive heat generation are some other reasons for the damage to the roller and ball bearings. These concerns can also be detected through Sonotec’s latest ultrasonic devices. Sonotec offers a combination of broadband ultrasonic testing devices and asset tree management software, providing robust broadband ultrasonic devices, intuitive apps, broadband sensors, and user-friendly management software (SONAPHONE DATASUITE) to achieve optimal efficiency in ultrasonic condition monitoring suites.
Why Choose Technomax for Ultrasonic Bearing Inspection?
With decades of experience, Technomax offers advanced Ultrasonic Bearing Inspection services using the latest ultrasonic testing devices from leading companies like SONOTEC. Our services are designed to detect the first sign of bearing faults, helping you avoid costly breakdowns and production delays.
Our advanced technology, together with the expertise of our skilled engineers, brings pinpoint accuracy in detecting bearing issues, whether lube failure, cracking, pitting or fatigue wear. Whatever the fault, you can count on us to keep your machinery running strong. Regular ultrasonic monitoring and testing allow you to gain critical insights into the health of your equipment bearing.
We have been partnering with reputable companies across the Oil & Gas, Power Generation, Petrochemical and other key sectors, delivering comprehensive condition monitoring services like Vibration analysis, dynamic balancing, acoustic emission testing, etc, tailored to meet the needs of your equipment and broader industrial requirements.
Being the leading engineering company in the UAE and the Middle East, Technomax can help you stay ahead with reliable, preventive maintenance solutions tailored to your industrial needs. Contact us today to schedule an ultrasonic bearing inspection.
Let's keep your bearing smooth!
Learn More About Our Services
Recent Blogs
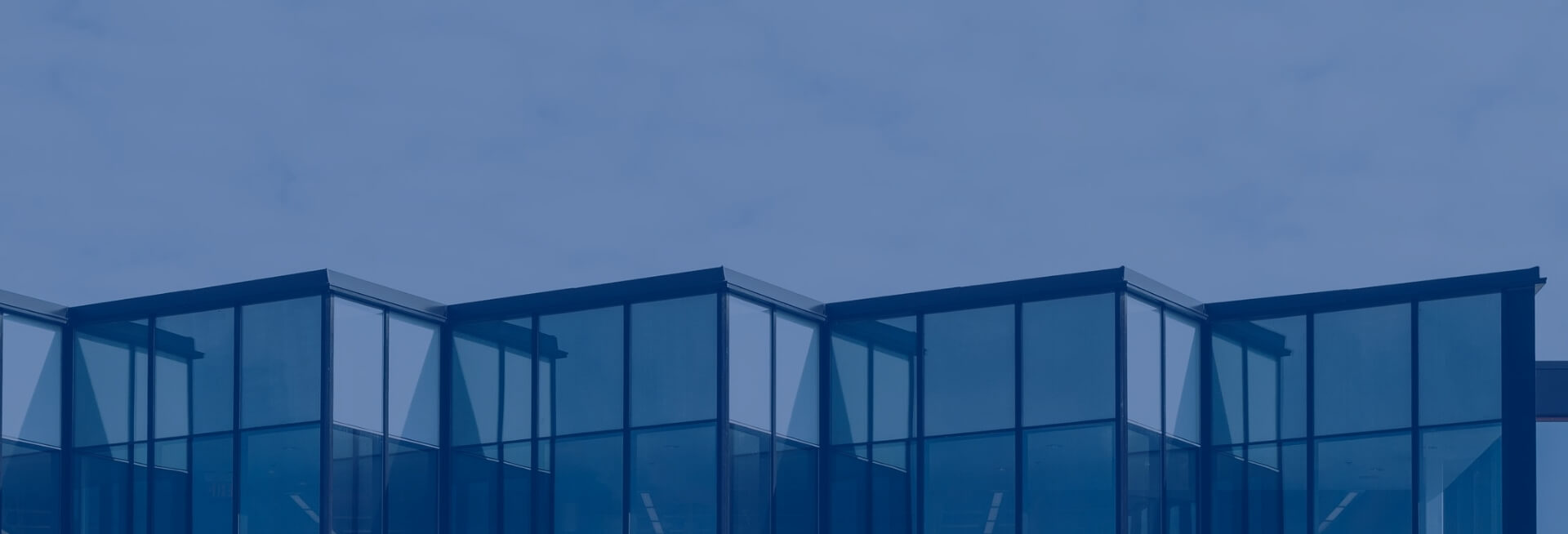
Get Started Now!
It takes less than a minute of your time. Or you may simply call +971 2 555 1 783