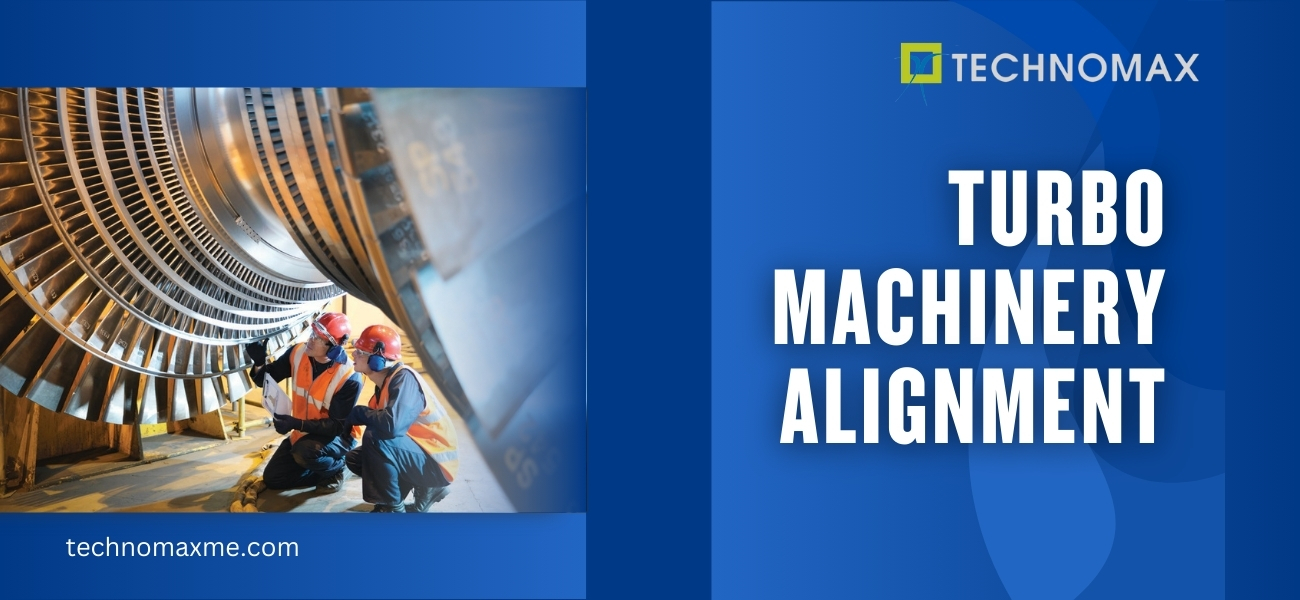
Turbomachinery Alignment for Long-term Preventive Maintenance
Turbomachinery Alignment is the process of positioning the shafts of the rotating parts of machinery such as turbines, generators, and compressors. When turbomachines transfer energy to or from a fluid flowing across them, the energy transfer is accomplished through the dynamic effect of fluid rotation around the machines’ axis. But why is it critical? Thousands of machines coupled with motors and countless rotating equipment need properly aligned shafts to work efficiently.
Alignment of Turbines: Understanding the condition of your rotating equipment is pivotal and is often understated despite being the cornerstone for your asset's reliability and optimal performance. One critical concern should be addressing a misaligned turbomachinery. Before going into the specifics, let us look at the basics of TurboMachinery Alignment.
What does the alignment of turbines entail? You can say turbomachinery is perfectly aligned when the centrelines of rotation of two or more shafts are lined in the horizontal and vertical plane. Simply put; they must be collinear. And so, any deviation in these relative positions leads to misalignment. This is never the case; the shafts are mostly misaligned. Turbo Machinery Alignment ensures the rotating parts such as turbines, compressors, and generators are well aligned.
This is crucial to facilitate smooth operations, minimise wear and tear, reduce vibrations and prevent probable failures.
Misalignment in Turbines
Several varieties of turbines exist in the industries: gas, steam, wind-powered and solar. Keeping them in excellent condition is inherent in the upkeep and continued operations in industries that rely heavily on machinery. Misalignment is the major reason for a turbine and rotating equipment to fail. Misalignments happen when two rotating shafts do not fall collinear, In most cases, through an angular gap, moderate offset gap or a combination of both.
When the rotating parts or the shafts are not properly aligned, significant vibration or shaft wobbling may occur, leading to excessive noise, overheating, rotor bending, reduced performance and even damaging the associated components such as seals, couplings, and bearings. If neglected, these issues may cause equipment failure, leading to costly downtimes necessitating replacement. Proper maintenance and regular alignment are important to avoid unexpected services and repairs.
Types of Misalignments
There are many shaft misalignments, each focused on how the shaft deviates from its normal alignment or disposition. A few common misalignments have been discussed below;
- Parallel or Offset Misalignment: occurs when the centrelines of shafts are offset horizontally or vertically, making the shafts parallel but not aligned. This type of misalignment is caused by manufacturing defects, improper assembly or wearing of bearings, putting stress on it, causing overheating, wear and premature failure.
- Angular Misalignment: occurs when the shafts are not parallel, but rather misaligned at an angle relative to each other. This misalignment is caused by shaft deviation due to excessive load or thermal expansion resulting in intensive wear on bearings, couplings and other parts.
- Angular + Offset Misalignment: It is a combination of both angular and offset misalignments, where the shafts are both offset and swerved at a relative angle caused by faulty installation, thermal fluctuation and equipment degradation. In general, this misalignment causes the most damage as it combines the effects of both angular and offset; causing severe vibrations, noises, wear and potential equipment failure.
- Shaft twist misalignment: occurs when the shaft undergoes a torsional twist, mostly due to uneven load distribution, poor coupling, or shaft deflection.
- Radial Misalignment: occurs when the shaft deviates from the desired radial centrelines, caused by damaged bearings, manufacturing defects, or deflection on the shaft due to uneven load.
Shaft or Coupling Alignment
As you may know, Shaft Alignment or Coupling Alignment are mostly used interchangeably, with a slight change in the focus on the aspect of the alignment process, the former refers to the process of aligning the shafts with each other on their axis, intending to achieve the smooth rotating of the shafts while the latter focuses on aligning the coupling that connects the shafts. However, in the field, they are usually done together.
Why is Alignment crucial? There are plenty of reasons, but few are listed here;
- Ensure rotor stability under different operating conditions
- Minimise extreme axial and radial bearing forces.
- Minimise mechanical seal failure.
- Reduce coupling components' premature wearing.
- Maintain desired rotor clearances internally.
- Reduce potential shaft failure from fatigue.
- Lower excessive vibrations in housings, bearings, and rotors.
Let us look at shaft coupling, its function in the drive train, and some features of different shaft couplings. Numerous shaft couplings are available in the market; from simple versions such as sleeve couplings to more intricate gear couplings. Shaft couplings connect two shafts to transmit the rotational motion and the basic function of shaft coupling is transmitting torque from the driver to the driven unit.
Shaft couplings ensure torque transmission, misalignment compensation, flexibility, shock absorption etc. Choosing the best shaft coupling based on factors like load, alignment, speed and operating conditions improves the reliability and longevity of the rotating machinery.
Turbomachinery Alignment Process
Here are the general steps involved in Turbomachinery Alignment:
Step 1: Preparation for safety - the equipment is shut down, isolated from power and inspected for any issues that may affect the alignment processes.
Step 2: Quick Inspection- Once the equipment is cleared off the power, a visual check is carried out to identify any mechanical damage (casings, bearings or couplings) and checks the machine foundation.
Step 3: Pre-Alignment tests- The machine is correctly positioned to rule out pre-existing distortions and verify the shaft and coupling conditions.
Step 4: Alignment Measurements- Initial alignment measurements are taken using the appropriate alignment method (Laser, Dial Indicator) and the shaft positions are measured.
Step 5: Adjusting Alignment- Based on the measured data, required shim or coupling adjustments are made, and axial displacements are also analysed.
Step 6: Verifying the adjustments - The adjustments are re-checked to finalise the desired level of tolerance. The tolerances depend on the type of equipment and the manufacturer's specifications.
Step 7: Post-Alignment tests- A trial run is made to monitor for vibrations, temperature variations and performance.
Step 8: Record and document- The alignment measurements, data and adjustments are recorded and documented for future reference.
Tolerance Variances
Misalignments of shafts create strain on the pumps and motors, damaging them and other parts like couplings, bearings etc. Tolerance levels or variances are established to understand the acceptable levels of shaft misalignment, it is the allowable deviation from a specific alignment.
Certain machines can work within specified tolerances; however, critical components like turbines and similar equipment are designed to work within desired tolerance levels, even minor misalignments can lead to significant issues like wear, vibrations and noises. In these cases, more detailed analysis and accurate alignment results are needed, which is where advanced precision alignment becomes essential.
Why is Precision Shaft Alignment Important in Turbines?
Unlike traditional alignment methods; Precision Shaft alignment should be integral to any preventive maintenance strategy. It involves much more meticulous processes with advanced laser alignment solutions or high-precision dial indicators to ensure the shafts and the components are aligned to a finer degree avoiding even small misalignments.
The slightest changes in the turbine flow rate, rotor speed, load & power, and noise levels can be duly identified and corrected through precision shaft alignment, preventing premature damage, and unscheduled operation outages to critical and sophisticated turbine components.
Gas Turbomachinery Alignment
While Turbine Machinery alignment focuses on the alignment of a wide range of turbine systems such as steam, wind, and hydroelectric; involving common alignments like a shaft or coupling, Gas turbine machinery alignment exclusively focuses on requirements of gas turbines, used generally in power-generating industries like oil, gas and aerospace.
Gas turbine machine alignment requires advanced and accurate techniques, considering high-speed operation, intense temperatures and specific clearance tolerances.
Being a service provider for the Oil and Gas Industry for nearly 2 decades, Technomax offers expert Gas turbo machinery Alignment. Our specialised gas turbo alignment services involve systematic strategies that start with an internal inspection, followed by partial disassembly to gain a deeper insight into the issues. Rotor-to-casing measurements are taken and recorded before any repairs are carried out.
Turbomachinery Alignment with Technomax
From this blog, we gained a better understanding of how Turbomachinery alignment is a quintessential service in industries, particularly in machine-intensive operations where precision is critical. Turbines, motors and other machine components need regular maintenance and proper care to prevent operational discrepancies, premature equipment failure, or unscheduled outages, with misalignment being the number one cause. Therefore, Precision Shaft Alignment using advanced tools is indispensable in identifying misalignments.
Technomax, a leading engineering company in UAE, offers exceptional condition monitoring services and customised solutions for all your turbine, motor, and rotating equipment needs. We provide the best Precision Shaft Alignment Services across the GCC to enhance your asset's performance and efficiency. By integrating modern tools and techniques with the expertise of our skilled technicians, we assure all-round protection for your equipment. Contact us now to learn how our alignment services can enhance your preventive maintenance strategy in the long run.
Learn More About Our Services
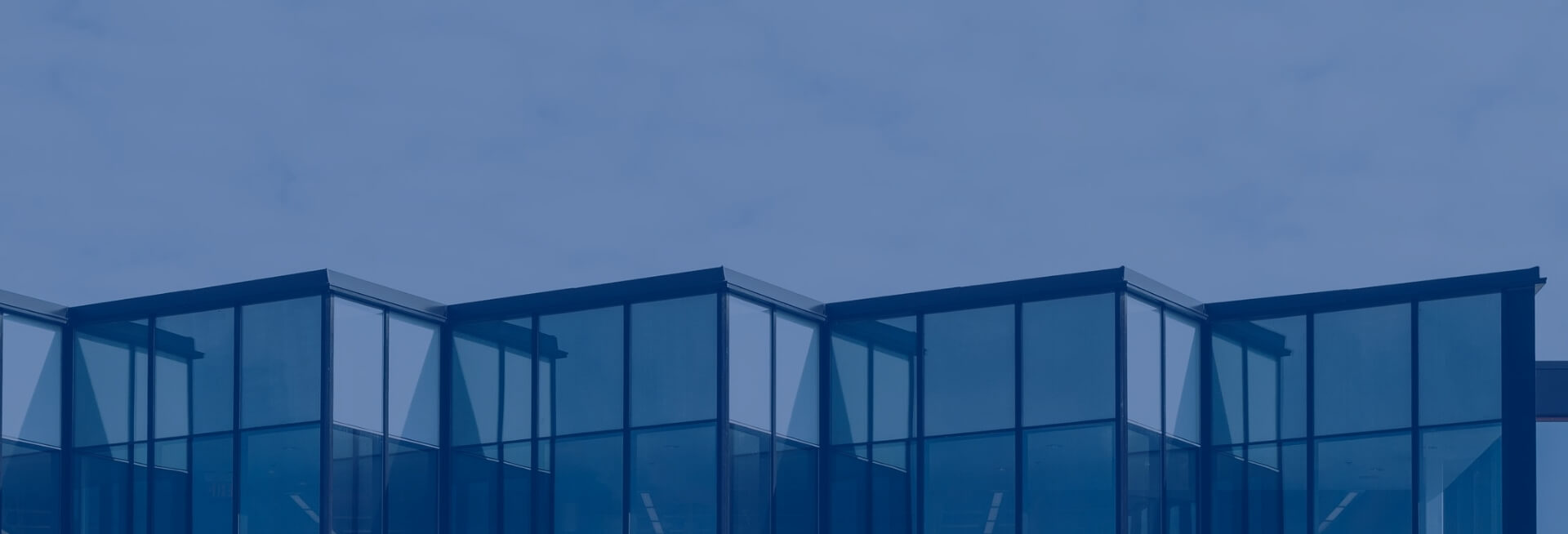
Get Started Now!
It takes less than a minute of your time. Or you may simply call +971 2 555 1 783