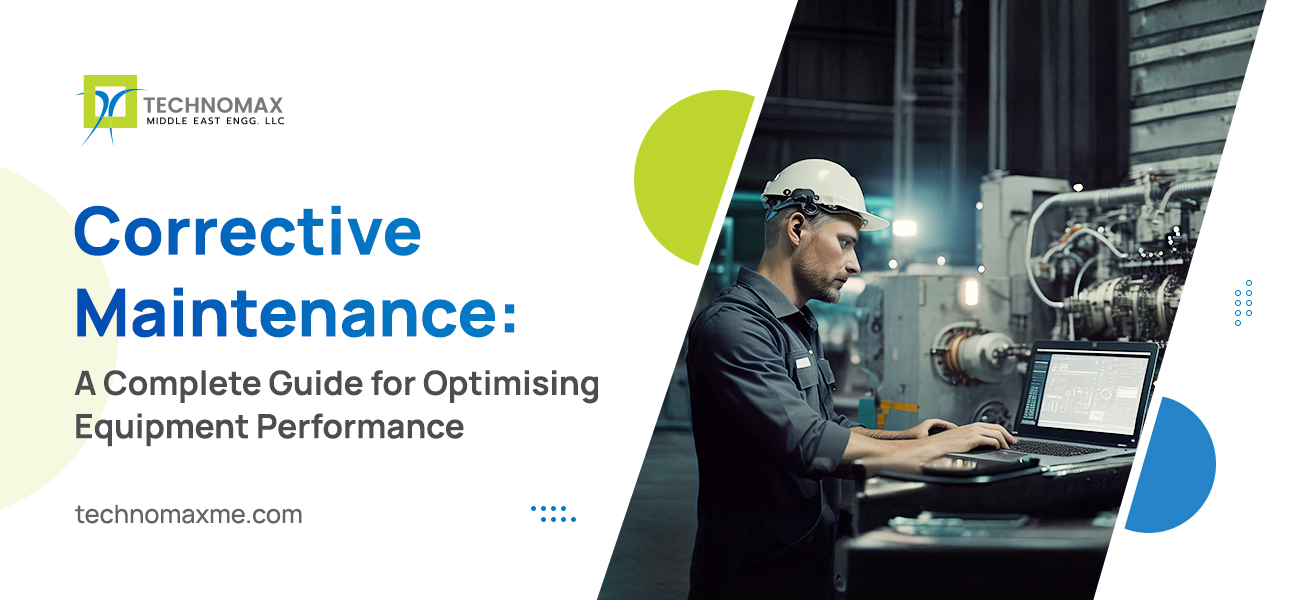
Corrective Maintenance: A Complete Guide for Optimising Equipment Performance
The production processes of every industry are unique, which is why efficient machinery management is essential. Let’s take an example of an active metal fabrication plant that requires reliable, modern manufacturing machines, such as Computer Numerical Control (CNC) machining centres, to ensure effective functioning. The CNC machines directly affect the productivity and quality of the plant. Even minor disruptions in their operation can trigger a chain reaction, leading to inefficiency, delays, and ultimately striking the company’s bottom line.
So, how can we address these challenges? The answer lies in corrective maintenance, which is important not only in the metal fabrication plants mentioned above but also in situations such as excessive noise from machinery, slow-performing software, or even broken or leaking water pipes. If we look for more, unclogging a drain, tightening a loose doorknob, rebooting your router, etc. are just a drop in the bucket compared to the many other corrective maintenance examples that arise in our day-to-day lives.
In this blog, we will explore everything about corrective maintenance, including practical implementation strategies and their significance within a comprehensive maintenance framework.
What Is Corrective Maintenance?
Corrective maintenance (also known as breakdown maintenance or reactive maintenance) addresses equipment or systems that have already failed or malfunctioned. The primary goal of this approach is to restore effective operation and minimise downtime to ensure continuity in operations. Industrial settings commonly use this approach, as equipment failure can interrupt production and result in financial losses.
In practice, corrective maintenance refers to remedial actions taken in response to failures or deficiencies found during normal operations or production to restore a machine or part of equipment to its operational state. This performance monitoring involves diagnosing the issue, identifying the underlying cause of the equipment failure, and implementing repairs or replacements as required. The ultimate goal is to address the immediate problem efficiently while keeping long-term reliability and performance in mind.
Workflow for Corrective Maintenance
Preventive Maintenance Performed
↓
Issues Detected
↓
Fast Fix
↙ ↘
Yes No
↙ ↘
On-site Repairs Create A Work Order
How Are Corrective Maintenance Needs Identified?
The three main types of maintenance tasks are breakdown, corrective, and preventive. While preventive maintenance is performed to prevent issues before they occur, corrective maintenance addresses issues that have already arisen. Identifying the right course of action is the first step to determine if corrective maintenance is essential. This involves regular inspections, monitoring equipment performance metrics, and analysing logs for past maintenance data. By closely monitoring equipment health indicators such as speed, pressure, vibration, temperature, fluid level, and other operating parameters, maintenance professionals can detect glitches, anomalies, or any early signs of impending failure.
Likewise, utilising preventive maintenance technologies like condition monitoring sensors and CMMS software helps get real-time information on the condition of assets. This enables businesses to forecast possible failures and glitches, allowing them to take preventive action. These measures not only reduce the need for corrective maintenance but also improve the overall reliability while extending equipment lifespan.
What Are the Different Types of Corrective Maintenance?
The corrective maintenance toolbox offers various options, each with its characteristics and purposes. The following are the main types of corrective maintenance:
- Emergency Corrective Maintenance: This emergency maintenance can be viewed as a fire drill or corrective maintenance - which means quick maintenance executed immediately following a critical system failure. The primary objective is swift issue resolution and restoring normal system or equipment functionality. This type of maintenance is frequently used for safety-critical systems or situations where failure poses a significant risk.
- Reactive Corrective Maintenance: This serves as an umbrella term covering all forms of maintenance initiated in response to failures or malfunctions. It includes emergency, immediate, deferred, and conditional maintenance practices.
- Immediate Corrective Maintenance: Swift and prompt action is required here. Immediate corrective maintenance is undertaken as soon as a failure is detected. Here, the purpose is to minimise downtime and prevent further disruptions or damage. Though not as urgent as emergency maintenance, it remains a high-priority response.
- Run-to-Failure Maintenance: As the name suggests, this strategy allows equipment to operate until a failure occurs, and run-to-failure maintenance is then performed in response. It’s commonly applied to non-critical or easily replaceable equipment, where the costs of preventive maintenance outweigh the cost of replacement.
- Deferred Corrective Maintenance: Not all situations require immediate attention. Corrective maintenance may be deferred to a more suitable time, such as during scheduled shutdowns or maintenance windows. This approach is typically chosen when the failure does not immediately impact operations or when resources are constrained.
- Conditional Corrective Maintenance: This approach relies on close equipment monitoring and assessment. Maintenance actions are triggered when specific condition indicators, like vibration levels or temperature readings, deviate from acceptable ranges, signalling potential issues. While often associated with predictive maintenance, it can also be considered corrective maintenance upon issue detection.
There are several types of corrective maintenance, each with special advantages and considerations. Each requires a strategy aligned with the equipment’s criticality, operational impact, available resources, and the overall maintenance strategy of the organisation.
When Is Corrective Maintenance Needed?
Corrective maintenance is required in various situations, including:
- Equipment breakdowns leading to production disruptions or downtime.
- Performance degradation impacting productivity, efficiency, or output quality.
- Safety concerns requiring immediate attention due to equipment failures posing risks to personnel or property.
Promptly addressing corrective maintenance needs is crucial to prevent further damage, maintain safety compliance, and ensure uninterrupted operations, especially in critical production environments.
How to Perform Corrective Maintenance?
Performing corrective maintenance involves a systematic, step-by-step approach with a focus on continuous improvement for maintenance:
- Identify the Problem: Conduct a thorough assessment to understand the root cause using diagnostic tools, maintenance logs, and expert analysis.
- Assess Scope and Resources: Determine the extent of repairs or replacements needed, evaluate resource requirements, and plan the maintenance schedule accordingly.
- Execute Repairs: Implement corrective actions following established procedures, guidelines, and safety protocols to ensure quality repairs and minimise risks.
- Test and Validate: After completing repairs, thoroughly test the equipment to verify functionality, performance, and safety compliance before returning it to regular operation.
Effective corrective maintenance requires collaboration between maintenance teams, equipment operators, and stakeholders. This facilitates knowledge-sharing and informed decision-making. Clear communication is also important to keep everyone informed about equipment issues, maintenance plans, and progress updates.
How Does Corrective Maintenance Improve Equipment Reliability?
A corrective maintenance programme goes beyond merely addressing breakdowns. It can be used as a diagnostic tool for long-term equipment reliability. A proactive approach focusing on the Overall Equipment Effectiveness (OEE) minimises costly downtime and repairs by focusing on early intervention, preventing minor faults from escalating into critical failures. The data collected from corrective actions directly informs preventive maintenance strategies.
Analysing these findings allows for identifying potential equipment weaknesses before they reveal major issues. This enables technicians to plan maintenance scheduling and optimisation focusing on equipment uptime and operational efficiency. Ensuring optimal equipment performance and maximising its operational lifespan facilitates a continuous improvement cycle.
What Are the Benefits of Corrective Maintenance?
Corrective maintenance provides a variety of benefits that improve equipment reliability, enhance operational efficiency, and promote cost-effectiveness.
- Cost-Effectiveness: Corrective maintenance can be a suitable strategy for less critical equipment as it minimises unnecessary maintenance costs and optimises resource utilisation by addressing problems only when they arise. However, it’s important to consider these cost-effective maintenance strategies against the potential costs of downtime and larger repairs if issues are neglected.
It can also be useful in identifying any underlying issues that may cause major problems in the future. Businesses can avoid future breakdowns by addressing these issues.
- Flexibility: The process of corrective maintenance is straightforward. This means it provides flexibility in handling diverse maintenance needs promptly and adapting to changing operational requirements and priorities.
Corrective maintenance ensures that when some issue arises, there are no complex procedures or schedules to follow other than identifying and repairing it. This can be particularly advantageous in situations where unforeseen equipment issues arise.
- Resource Optimisation: Since corrective maintenance is reactive, it can be considered a suitable strategy that doesn’t require extensive planning or scheduling of maintenance tasks. While it offers minimal downtime impact, inexpensive equipment repair, and low failure rates, it also frees up time and resources for other activities.
This helps organisations to utilise their maintenance resources efficiently and allocate them strategically based on criticality, impact, and available expertise. This ensures critical equipment receives prompt attention, while less critical issues can be addressed during planned downtime.
Consider the same example of the CNC machining centre we talked about in the introduction. Imagine that it experiences a spindle motor failure. Prompt corrective maintenance restores machine functionality and prevents production delays and revenue losses associated with downtime.
Corrective Maintenance vs. Preventive Maintenance: Understanding the Differences
Understanding the differences between corrective and preventive maintenance plans is key to establishing a strong equipment maintenance strategy:
- Corrective Maintenance: This reactive approach, corrective maintenance, prioritises fixing equipment failures after they occur. By analysing data through performance monitoring, technicians aim to restore functionality promptly and minimise downtime. However, it’s important to note that corrective maintenance itself doesn’t directly improve equipment reliability. Its benefits come into play after a failure has happened.
- Preventive Maintenance: This proactive approach prioritises preventing failures altogether. Through regular inspections, servicing, and part replacements (like lubrication, filter changes, and vibration analysis), potential issues are identified and addressed before they escalate.
Preventive maintenance is vital in reducing unexpected breakdowns and plays a more strategic role than corrective maintenance. It helps detect problems early, which reduces the frequency of failures, optimises equipment performance, and extends the equipment life cycle. With the help of machine learning, it can analyse equipment data and predict future issues, which enhances preventive maintenance even further.
Corrective Maintenance vs. Preventive Maintenance
Feature | Corrective Maintenance | Preventive Maintenance |
Approach | Reactive | Proactive |
Planning Required | Low | High |
Downtime | Unpredictable and potentially lengthy | Minimal planned downtime |
Costs | Potentially lower upfront costs, but higher long-term costs due to breakdowns | Higher upfront costs, but lower long-term costs due to fewer breakdowns |
Suitability | Less critical equipment | Critical equipment or equipment where breakdowns are costly |
CMMS software for corrective maintenance makes repairs efficient and reduces downtime by streamlining the process of responding to breakdowns. The combination of machine learning and CMMS software along with a well-balanced approach to both preventive and corrective maintenance, ensures comprehensive maintenance coverage.
How to Reduce the Need for Corrective Maintenance?
The more often an asset breaks down, the more expensive it becomes to operate. Here are some strategies to reduce corrective maintenance needs and achieve a more proactive maintenance approach:
- Establish Proactive Maintenance Schedules: Develop and implement schedules based on equipment reliability data, operational demands, and historical maintenance data. These schedules should outline routine inspections, servicing procedures, and recommended replacement intervals for critical components.
- Conduct Regular Inspections: Perform routine inspections, condition assessments, and performance evaluations to identify potential issues early and address them proactively. Early detection allows for timely corrective actions and helps prevent minor problems from snowballing into major failures.
- Invest in Predictive Maintenance Technologies: Utilise advanced technologies like condition monitoring sensors, predictive analytics, and machine learning algorithms to predict failures, anticipate maintenance needs, and take preventive actions. These technologies can provide valuable insights into equipment health and enable organisations to schedule maintenance interventions before failures occur.
- Continuous Improvement: Continuously evaluate maintenance processes, performance metrics, and feedback to identify areas for improvement. By fostering a culture of continuous improvement, organisations can refine their maintenance strategies, optimise resource allocation, and enhance overall reliability and efficiency.
- Train Staff on Equipment Care: Provide comprehensive training and resources to equipment operators, maintenance personnel, and stakeholders on equipment care, maintenance best practices, and safety protocols. Educating staff empowers them to identify potential issues early on, operate equipment properly, and report problems promptly, all of which can contribute to reduced corrective maintenance needs.
By taking a proactive approach to maintenance, organisations can contribute to continuous improvement and implement effective strategies to achieve sustainable operational excellence. This will not only help to reduce corrective maintenance needs and minimise downtime but also enable businesses to operate more efficiently and effectively.
Being the leading engineering company in UAE, Technomax offers reliable condition monitoring services like infrared thermography testing, partial discharge testing, acoustic emission testing, etc. Our team of experts at Technomax can help you develop a customised maintenance plan that optimises equipment performance, minimises downtime, and maximises your return on investment. For more information, get in touch with us now.
Learn More About Our Services
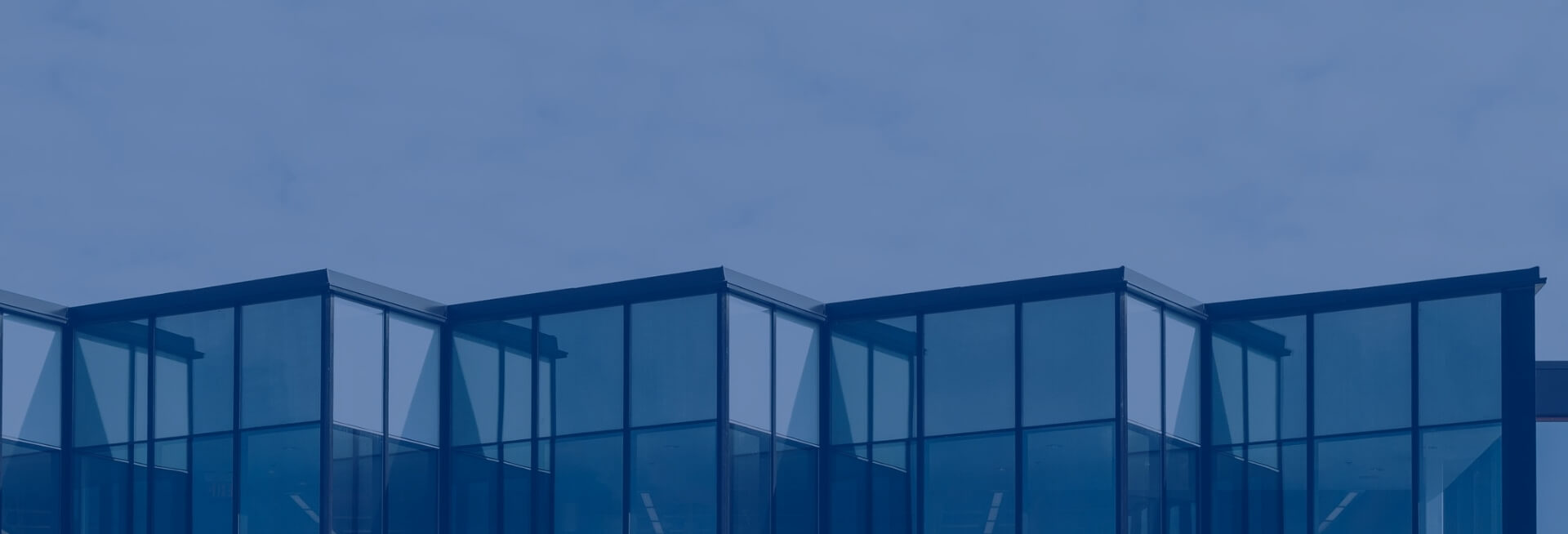
Get Started Now!
It takes less than a minute of your time. Or you may simply call +971 2 555 1 783