
Dynamic Balancing Of Gas Turbine Rotor
The dynamic balancing process of rotating components is a significant factor that helps the manufacturing and maintenance of turbomachinery. Unbalanced rotating equipment causes numerous operational concerns, which might impact the timely start-up of the facility.
Additionally, the unbalanced equipment results in internal damage which can affect the design efficiency, minimize the machine reliability, and cause a rise in the costs of operations and maintenance. This blog takes you through the dynamic balancing of gas turbine rotors, their functioning, and their benefits in detail.
Read more about:
- What is Couple Unbalance – Definitive Guide
- Preventive Maintenance Using Vibration Analysis in Electric Induction Motors
- Rotodynamic Analysis Services from Technomax
Understanding Rotor Balancing
A gas turbine employs natural gas and enables the conversion to mechanical energy. This combustion engine drives the generator, which builds electrical energy. Electrical energy flows through the power lines to businesses and homes. Gas turbine rotors augment power generation in various industrial applications like aircraft, electric generators, motor pumps, ships, compressors, tanks, etc.
Balancing is the process in which the mass distribution of the spin axis gets evaluated and corrected if required. This helps to maintain the bearing forces and the shaft vibrations corresponding to the operating frequencies in the confined limits. Unbalance is the major factor that causes vibrations in the rotor. Balancing avoids the vibrations due to the unbalance, and makes sure the rotating equipment is safe.
Rotor dynamic balancing has a prime effect on the productivity and life of every rotating machine. The extent to which a rotor stays out of balance is ‘unbalance’. The rotor imbalance builds force on the bearing assembly which causes heat, noise, and vibrations thereby impacting the performance of the machine.
Hence, the ideal solution would be to eliminate all causes of vibration and let the machine operate smoothly. Balancing involves removing or adding weight to the device so that the effective mass centre reaches the true axis.
Evolution of Dynamic Balancing
Earlier, low-speed rotor balancing was the only option since the turbine rotors were maintained either in the facility or had no access to high-speed balance systems. Relying on a low-speed balance can lead maintenance experts to miss many issues– for example, the power plant experts know that in certain rotors the turn-to-turn shorts appear at either the rated speed or near this speed. So, a machine without high-speed balancing can cause vibrations, which can damage the rotating parts, thereby forcing undesirable outages. The maintenance engineers have reported that the high-speed balancing lowers the vibration levels, minimizes the problems with the bearings, and reduces the wear and tear of units.
Different Dynamic Balancing Techniques
Depending on the system, single-plane balancing and dual-plane balancing techniques are used. Choosing one-plane or two-plane balancing relies on two different factors. The ratio between the length (L) of the rotor and the diameter (D) of the rotor is one of the most important factors. Another aspect is the operating speed of the rotor.
Single Plane Balancing
This technique includes the process of placing weight in a plane to gain an appropriate level of balance. The balancing process performed without spinning the rotor up to the specified operating speed is termed single-plane balancing. This technique adopts 3 steps:
- Measure the initial amplitude and phase of vibration unbalance.
- Trial round to add the known trial weight at an arbitrary location and record the corresponding variations in the phase and amplitude of the unbalance.
- Calculate the correction weight and location in the final stage.
Dual Plane Balancing
If we consider balancing the two planes, this is similar to the process of a single plane balancing process. Dual-plane balancing focuses more on the interference of the correction plane and the cross-effect characteristics.
Two planes rotating balance is the ideal method you can use to balance the impellers while the width-to-diameter ratio exceeds 0.50. When you make the corrections in a single plane, the plane separation becomes impractical with the narrow width of the propeller fans and the impellers.
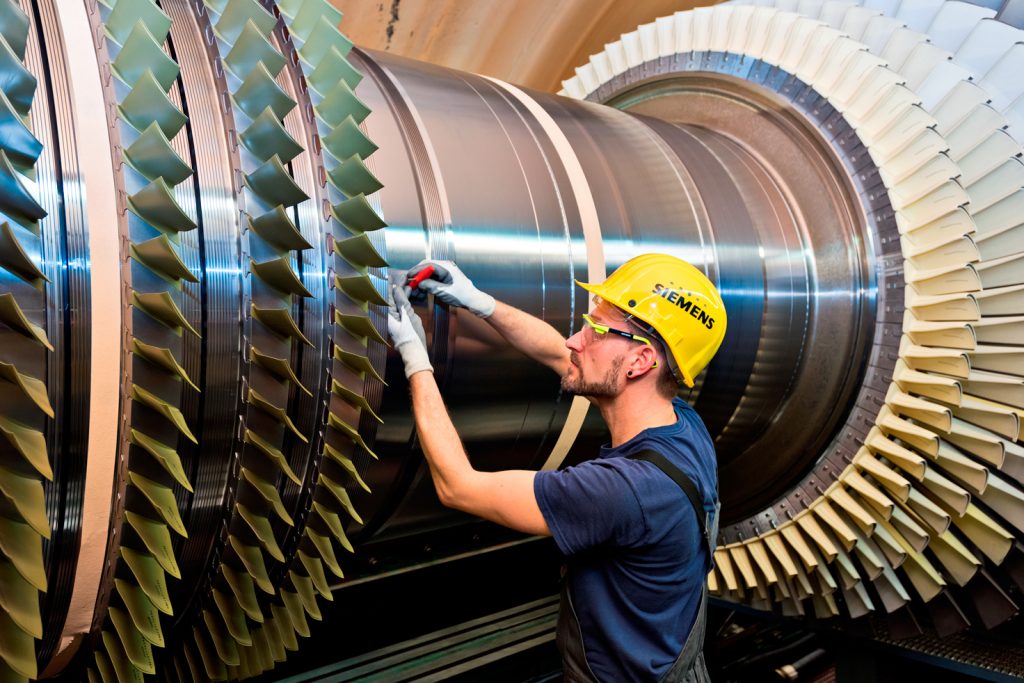
Measurement & Analysis Methods
Balanced rotors are significant to support most types of rotating equipment. Unbalance causes high vibrations, reduces life, and causes defects in equipment. In most circumstances, the rotor unbalance is the root cause of the vibration, and is well related to the rotational frequency. The objective of balancing is to reduce the vibrations concerned with the first order.
Torsional Vibration analysis is the initial step you should adopt before the next step, i.e., the rotor balancing. Rotor imbalance is the usual defect that produces excessive machine vibrations. Hence, anyone who needs to understand the dynamic behaviour of the system in operation should have a reasonably good understanding of this process. This is also important to adopt a predictive maintenance program.
Dynamic Balancing Process for Gas Turbine Rotors
Here is a step-by-step guide on the dynamic balancing technique of gas turbine rotors:
Prepare the turbine elements and rotor to perform the balancing
Adjust the rotor speed and record the unbalance at every speed. Choose and record a specific rotor speed, which will stay constant for the entire experiment. Note that this speed applies to the final results to correct the balancing weights. The results you obtain while using a lower speed can be further evaluated with the help of higher speeds.
Create initial measurements and find the unbalance
Record the vibration amplitudes at either bearing with the exact rotor mass unbalances. Determine the masses needed at either plane of the rotor to implement dynamic balancing of the rotor. You manually perform these calculations initially, then evaluate them using digital measurements.
Calculate correction weights and understand the placement
Add correction masses and run the rotor. Record the amplitudes of vibration at the two bearings. Calculate the correction masses and locate the placement of these weights.
Add the trial weights and measure the effectiveness of the balance
Choose the trial weights arbitrarily and mount them on one plane of the rotor at 00 angles. Record the readings at the two bearings. Follow and repeat these steps with trial weights at 900, 1800, and 2700 angles. Repeat the steps with the trial mass mounted at the other plane of the rotor and calculate the readings. Mount the trial weight at 450 on the initial plane and record readings at the two bearings. This reading is not necessary for rotor balancing but can be used to check the calculations later.
Why has the technique of Dynamic balancing become important?
- Increased customer demand: Let’s consider an example here: The liquid-condensed units with 400 MW and higher were not designed to cycle. However, the changes in the market have changed the unit dispatch rates, thereby favouring renewable energy resources. Regardless of its compliance with stringent mandates or the response to the price signals of fuels, the unit cycling has caused serious maintenance issues. Since dynamic balancing can potentially reduce maintenance concerns, it evolves to become an integral part of the maintenance outage planning for power generators.
- High-speed balancing features: Operators highly prefer the high-speed balance on the turbine rotor for returning the unit to action. With technological advancement, the cost-effective alternative includes using the vacuum capability and the feature to excite the rotors at increased speed. It streamlines the testing and balancing of the gas turbine rotors. This also reduces the outage cycle of the unit and helps the machine to come back online faster.
- Fast Turnaround: The usual repair cycle for the rotor includes pulling it right from the start and moving it to the maintenance site. If the rotor needs a complete rewind, the cycle can extend from 20-30 days based on the size of the generator. The cycle reduces to below 10 days if it only involves testing and inspecting the unit. Even when the unit turns offline and comes back to the full load in the specified number of days, the regulatory review for an outage can be desirable.
You may also like to read:
- Vibration Motion Magnification by Technomax
- Equipment Performance Monitoring – Our Approach
- Electrical Preventive Maintenance and Scalable Services
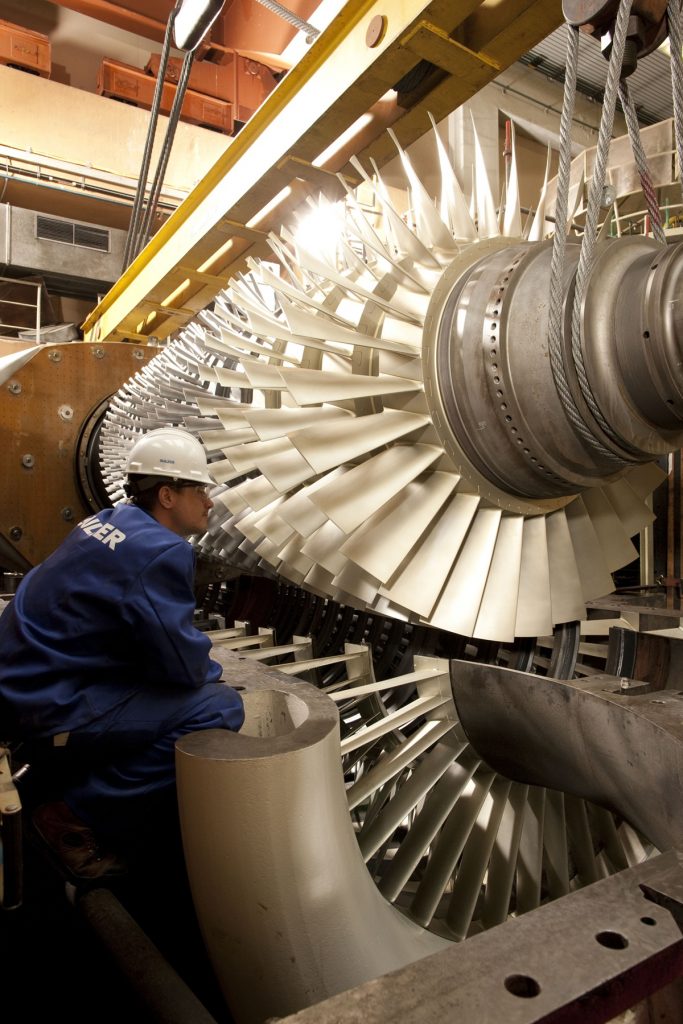
Core Benefits of Implementing Dynamic Balancing
Improved Turbine Efficiency and Performance
Balancing removes the vibrations and ensures they operate uninterruptedly. With dynamic balancing, the turbines work with high efficiency and also make certain that the components exhibit great durability. With the application of the highest centrifugal force the equipment experiences during the service, it lets precision balancing of equipment to a constant base point.
Minimization in the vibration levels and the potential risks
Since the vibration that results in airborne noise is not present, performing dynamic balancing causes a reduction in the noise levels. Additionally, balancing also lets you address the operator concerns caused due to the exposure to vibration and excessive noise. This procedure further helps to scale the efficiency of the operator.
Increased lifespan of the turbine components
The unbalanced rotors need high energy to perform tasks similar to the well-balanced rotors. The vibrations produce excess heat which should be also addressed while considering the system. Balancing machines can improve the life of the bearing. It is significant to note that this causes an imbalance that the nearby structure absorbs. While a machine operates in balance, it reduces structural stress. The increase in uptime enhances the productivity of the machine.
Cost savings with the reduced maintenance and increase in reliability
Operating the unbalanced machine incurs additional operating expenses. You should not only maintain the rotors to ensure backups during failure but also consider the costs. A utility based in Ohio said that it spent almost 180,000 USD per run-up to restart after the outage. On the contrary, the facilities which use high-speed balance technology such as thermal testing use reduced costs.
Scales the speed and effectiveness of testing
Operators usually face problems with the shorted turns in the rotors, which causes changes in vibration with the thermal action and heating up of the parts. The dynamic balancing method helps to perform a flux probe test which makes sure there are zero shorts with speed as the unit makes it back to the service. It also makes the thermal test or heat run effective– this involves the assessment of the quality of windings, where the operator can ensure the quality of the windings according to the ability to grow with the load symmetrically.
Technomax Approach in Providing Dynamic Balancing Services
At Technomax, we offer dynamic balancing services in the UAE for rotating machines and gas turbine rotors. If your company is into overhauling the impeller, or from a production/process industry, we have a team of specialized professionals who focus on considering your precision balancing requirements.
The rotating machinery such as engines, turbines, and generators which operate at a high range of pressure and temperature get susceptible to periodic wear and tear. They need balancing at the specific schedule to control the vibration levels to particular limits. To get the best dynamic balancing services for your industrial equipment and discuss more about the way we work, contact us today.
Learn More About Our Services
Recent Blogs
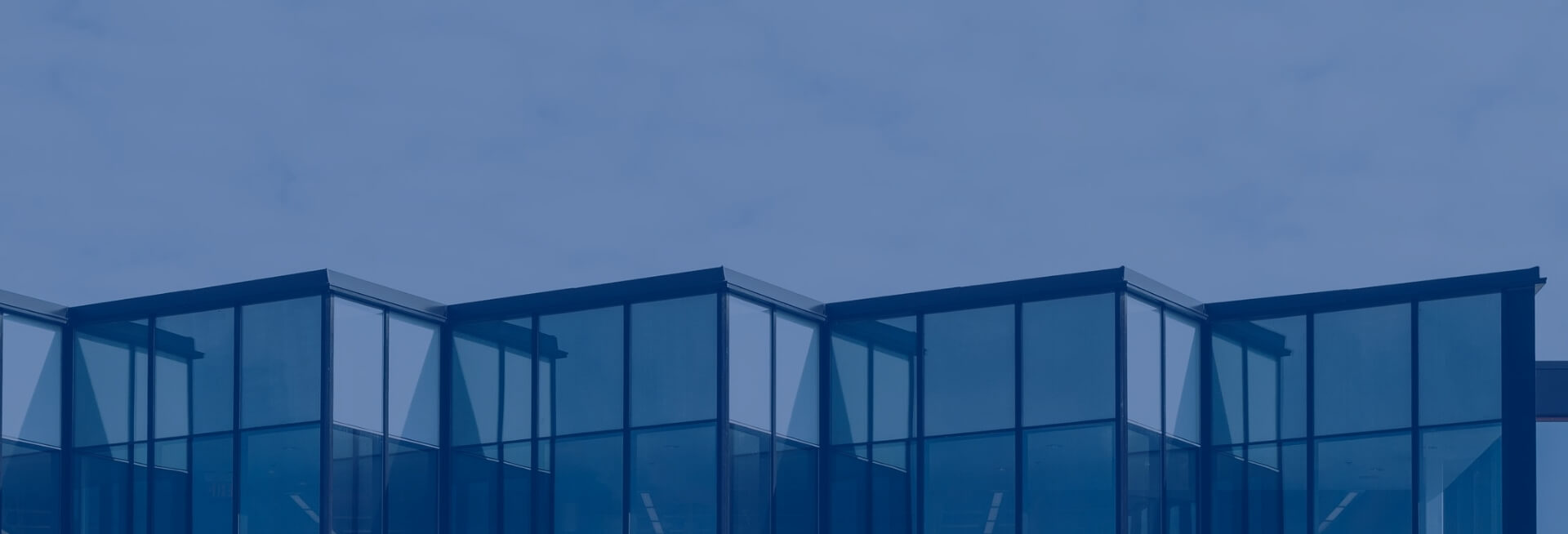
Get Started Now!
It takes less than a minute of your time. Or you may simply call +971 2 555 1 783