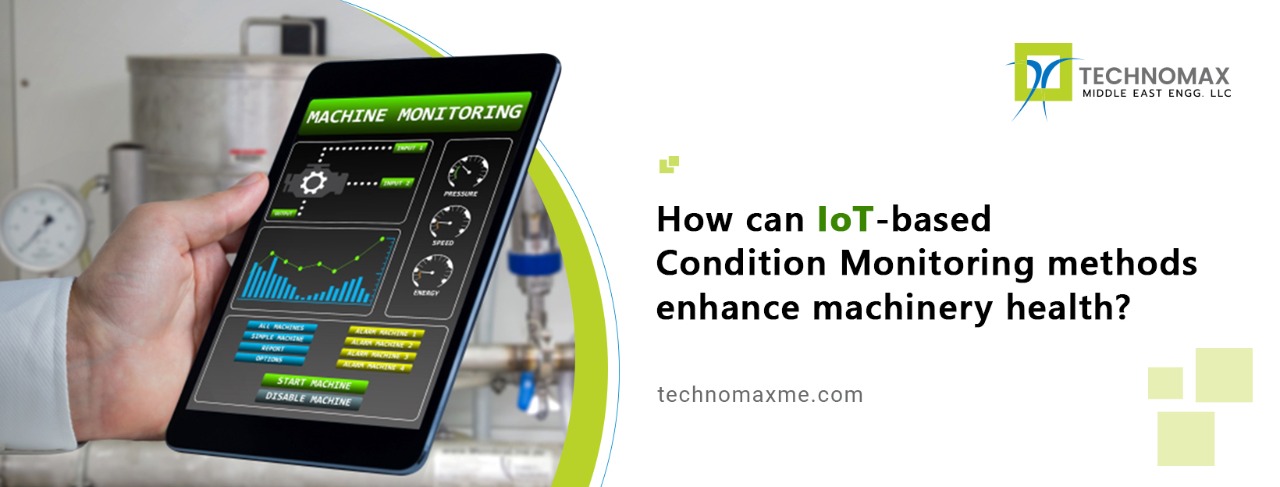
How Can IoT Condition Monitoring Methods Enhance Machinery Health?
Keeping product quality high is a major production objective. However, this goal still appears to be impossible for many businesses. Frequently, problems with a product's quality aren't discovered until it fails a test or, worse when a client returns it or causes an issue.
Faulty equipment that has not been properly maintained or calibrated is a frequent reason for decreased product quality. IoT-driven machine status monitoring is becoming more and more popular among manufacturers since it enables early detection of equipment problems that may compromise product quality.
Read more about:
- Radio Remote Control for EOT Crane
- Why Do Steam Traps Fail: Causes, Factors & Preventive Methods
- Yamada Air Operated Double Diaphragm Pumps – Yamada AODD
What Is the Methodology of IoT Condition Monitoring?
An essential component of an industrial maintenance plan is IoT Condition Monitoring. It concentrates on input, output, and impact to monitor any issues or ongoing wear and tear. The monitoring system emphasizes the analysis, interpretation, and reporting of the measurement points of your important machinery using big data through the network and sensors.
Basic IoT Condition Monitoring Test Parameters
- Vibration
- Speed
- Lubricant analysis
- Ultrasonic emissions
- Environmental characteristics such as temperature and air pressure
What Role Does IoT Play in Condition Monitoring?
- IoT assists in directing all data to the server for additional analysis. As a result, a practical, quick, and secure management platform will be made possible
- The Internet of Things is used in monitoring to link all the equipment together
- It works to manage and keep track of the equipment's power and efficiency
- Important and powerful equipment, including asynchronous motors, blowers, compressors, conveyors, and pumps, is kept under control
- Machine testing by hand is no longer necessary owing to IoT condition monitoring
- Businesses no longer need to inspect and monitor every device owing to the power of IoT
- This also has advantages in terms of scalability, connectivity, and time savings
- It offers complete internet protection and monitoring services
Other Advantages of IoT Condition Monitoring
- Increases life expectancy, lowers storage and maintenance costs and eliminates the need for costly repairs and repair time
- It establishes standard operational conditions
- Efficiently manages each piece of equipment's maintenance schedules
- Detects faults with enough time to rectify them successfully
- Checks for new updates and license renewals
- Ensures operational safety
- Aids in restricting and monitoring worker access to equipment
- Boosts output
Leveraging IoT to Drive Product Quality Control
Condition monitoring enables product quality control by detecting combinations of equipment health, such as engine temperature, spindle vibration frequency, cutting speed, and environmental parameters, such as temperature and relative humidity. When these elements come together, a product's output quality could be affected.
You may also like to read:
- Importance of Limit Switches in EOT Cranes
- Reliability Centered Maintenance - Simple Guide
- Vibration Structural Analysis - Ultimate Guide
IoT Condition Monitoring in Different Industries
Industrial IoT enables businesses in the pulp and paper sector to keep tabs on the health of the rollers in paper mills. Any uncertainty in a single roller bearing can impact the paper's quality, cause fluffing, and alter the paper's thickness. A significant portion of quality problems may be avoided by integrating vibration sensors for condition monitoring into roller bearings.
In the automobile sector, temperature changes in welding equipment can result in a failed weld connection, while moisture infiltration into the crevices and gaps in welded regions can cause porosity. Incorrect placement may be greatly reduced and the excellent quality of the welded products can be guaranteed by using industrial IoT to monitor the temperature and humidity level surrounding a machine.
Conclusion
Regardless of the fact that IoT condition monitoring opens the door for higher levels of production quality, this strategy has certain drawbacks since precise quality assurance may not be attainable without knowledge of the state of the machine. A machine's health management and monitoring system can be done by IoT-driven condition monitoring. You can gather a lot of data with the aid of CPS, sensors, and equipment. A machine learning algorithm for predictive maintenance can be conducted with this amount of data. Organizations can now forecast machine failure with real-time data, solutions, and transparency. This will put a stop to any conceivable operational outage or shutdown. For instance, problems brought on by the use of faulty or inadequately labeled components or incorrect material handling cannot be detected by checking machine status. Regardless of the time period, it is imperative to consistently and routinely inspect the equipment for emissions, whether it is susceptible to deterioration or fast upgrades.
Your progress is accelerated by the Internet of Things and condition monitoring. Additionally, it offers superior services with a high level of security. Product quality may be managed to increase output, decrease scrap, and limit rework by keeping an eye on the health of the equipment used to make them. The IoT condition monitoring strategy may not give as much distinction in terms of quality control scope as other quality assurance strategies, but it can assist in identifying quality issues at an early stage and anticipating possible ones.
Learn More About Our Services
Recent Blogs
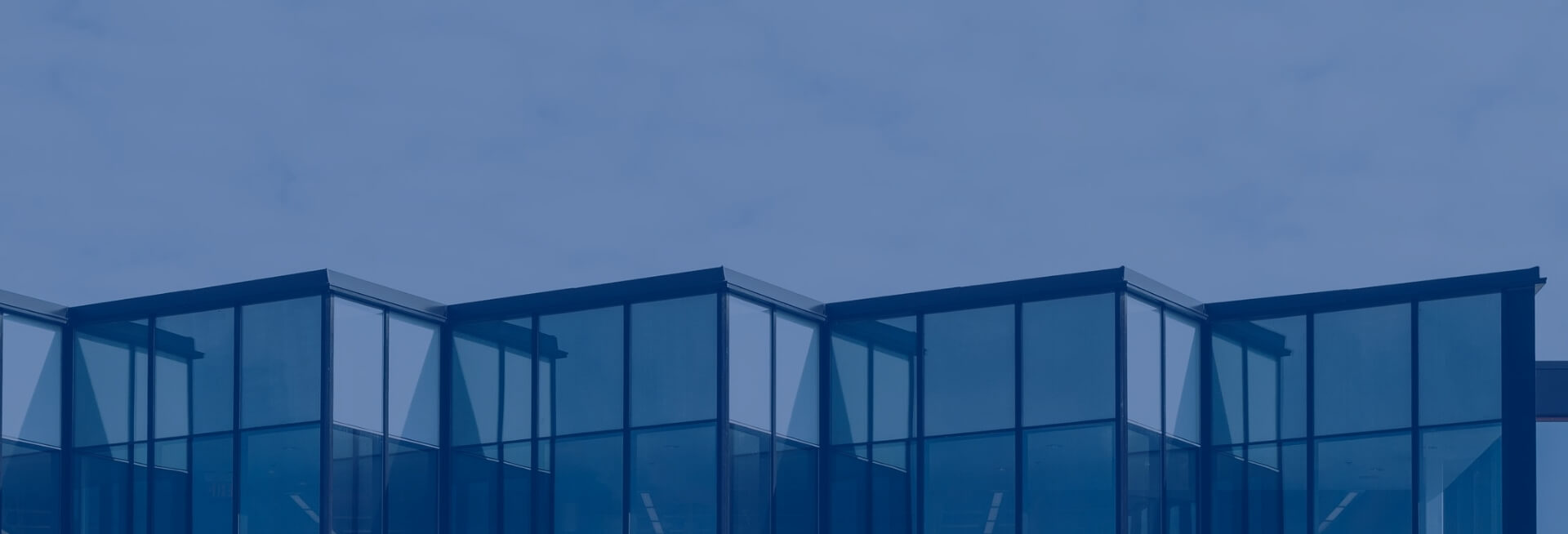
Get Started Now!
It takes less than a minute of your time. Or you may simply call +971 2 555 1 783