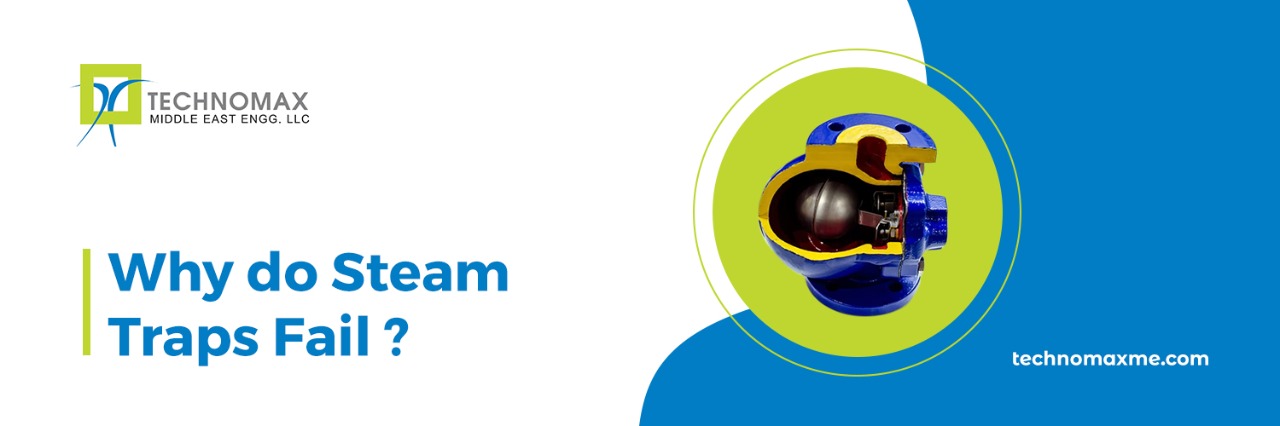
Steam Traps Fail: Reasons, Factors Affecting, and Preventive Methods
Many plant managers are concerned about steam trap failure. Steam trap failure degrades the performance of steam systems and poses a safety threat. Steam trap failure can be caused by a variety of factors. It would be beneficial to go over a couple of them and learn how to prevent them.
What is a Steam Trap?
A steam trap is a component of a steam system used in steam-heated operations in plants and factories and steam-driven turbines in power plants. Steam traps are an automatic valve that filters away condensate (steam that has condensed) and non-condensable gases like air while allowing steam to escape.
Steam is frequently employed in industry for heating or as a mechanical driving force. When water evaporates into a gas, steam is generated. The water molecules must be given enough energy (heat) to break their bonds in order for the evaporation process to happen. Latent heat (the energy required to transform a liquid into a gas) is used in steam-based heating processes and transferred to the product. The steam condenses and produces condensate when the process is complete since condensate cannot perform the same tasks as steam.
If condensate is not evacuated as quickly as possible, heating efficiency declines in steam transport piping or heat exchangers.
Steam traps serve three primary purposes:
- As soon as the condensate forms, discard them (unless it is desirable )
- To minimise steam usage, i.e. be energy efficient
- Air and other non-condensable gases can be disposed of using them.
Steam is typically dry when it leaves the boiler house. Radiation losses and condensate formation occur as steam flows through the pipework. During heating operations, steam loses heat to the heated items, resulting in condensate formation. Steam traps have a critical role in eliminating condensate as soon as it forms.
You may also like to read:
- Yamada Air Operated Double Diaphragm Pumps – Yamada AODD
- Reliability Centered Maintenance - Simple Guide
- Brief Note on Vibration Structural Analysis
Types of Steam Traps
- Mechanical traps
These use the mechanical characteristics of steam vs condensate to extract condensate. Usually, the liquids will sink to the bottom of the system since it is denser than steam. A bucket or float rises and falls in proportion with the condensate level in mechanical traps. This is frequently connected to a mechanical linkage that opens and closes the valve.
- Thermostatic traps
The temperature difference between the steam and liquid phases eliminates condensate in this type of trap. The valve is controlled by the expansion and contraction of an element exposed to steam or condensate heat. To open and remove condensate, these traps require a temperature drop below the saturation curve. This can be accomplished with a filled element, bellows, or bimetallic element in these traps.
- Thermodynamic traps
The dynamic concepts of steam vs condensate and Bernoulli’s principle are used in this trap. Condensate is released via an opening at a faster rate, resulting in a pressure drop. This will cause a burst of steam to provide enough pressure to close a valve (disc) or slow the trap’s discharge speed.
Failed steam traps have the following negative impacts:
- Affects the entire steam system
- It's a waste of energy
- Production decreases
- Maintenance costs rise
Traps are adversely affected by three general conditions:
- Dirt is the most common cause of failure, resulting in a leaky or plugged trap.
- Water-hammer and consequent damage to the internal steam trap components due to pressure surges (due to sudden steam valve openings, faulty pipework, or trap misapplications).
- Oversized IB traps may lose their prime, whereas TD traps may experience rapid cycling.
When a steam trap fails, the condensate is improperly removed. The annual failure rate of steam traps in some steam systems can be as high as 35%. As a result, it's critical to comprehend the causes of steam trap failure. The following are some of the reasons that cause or hasten the failure of steam traps:
Reasons for the Failure of Steam Traps
1. Contamination of Feed Water
Carryover is caused by improper feed water treatment, which contributes to steam trap failure.
2. Steam Traps Installed Incorrectly
Some steam traps include built-in strainers, while others require the installation of a separate strainer before the steam trap. In the absence of a strainer, rust or other debris may be entrained inside the trap, causing damage to the trap's internal system.
3. Inadequate Maintenance or a Lack of Maintenance
Every steam trap necessitates regular maintenance. Steam trap maintenance has been noted to be either badly performed or altogether absent at numerous plants. Every steam system should have a maintenance schedule that must be adhered to.
4. Condensate Contamination
Condensate pollution occurs when heat exchangers leak or when several utilities are used. Condensate contamination can lower the pH and make it acidic. Acidic condensate corrodes the internals of steam traps, which is one of the reasons why they fail.
5. Choosing the Incorrect Type of Steam Trap
Selecting the steam trap is the most important step in determining a steam trap's performance and operating life. Frequently, the incorrect type of steam trap is fitted to the incorrect application. As a result, the steam trap's lifespan is reduced.
How to Prevent Steam Traps from Failing?
- Conduct a steam trap survey regularly.
- Identify flaws in the system's design.
- Conduct an insulating inspection. The cost of steam production will be increased in areas where insulation has been removed and never reinstalled.
- Check for bypass valves in your steam system using ultrasonic detection equipment. They could be leaking when they should be shut down.
- Seasonally operated equipment, such as unit heaters, should be turned off.
- Using a hand-held IR temperature analyzer and an ultrasonic leak detector, test control valves or shut off valves in the HVAC system should be analyzed regularly. They increase overall energy expenses, even if they are partially leaking.
- Examine the system and inventory equipment that isn’t in use. Remove any systems that are no longer functional.
- Use a computerized system to manage and analyze processes whenever possible and practical.
The efficiency and operating life of steam traps will considerably improve if the concerns stated above are avoided and the steps are followed.
What is a Steam Trap Inspection?
Leaks, both to the atmosphere and through valves and steam traps, become a major source of waste and inefficiency. Preventing steam leaks and maintaining steam traps are two ways to improve a steam system.
The prime objective of a practical steam trap inspection system is to repair any malfunctioning steam traps or steam leaks that can compromise safety, energy efficiency, and quality.
A successful steam trap maintenance program should also include properly training employees to effectively execute the steam trap inspection.
To increase the overall effectiveness of the steam trap survey, knowing what the potential problems are and how to identify them is essential—having a strong understanding of how the steam system works can also help the inspector spot any faults when performing the steam trap survey.
The Future of Ultrasonic Steam Trap Testing
When it comes to steam trap preventive maintenance, it's safe to claim that the SONAPHONE digital ultrasonic testing devices and SteamExpert app are indeed the best. They've combined everything into a single user-friendly software package. So you won't have to bother with human errors, missing reports, or stacks of paperwork anymore.
With it, you can also test all types of steam traps, whether thermal or floating, using a combination of ultrasonic and temperature data.
All an inspector needs to do is connect the sensor and activate the SteamExpert app. A long waveguide is used for testing, allowing you to observe the steam trap safely from a distance. The SONAPHONE records the ultrasonic signal within the set range. The inspector can tell if the steam trap is working correctly or not by looking at the screen and the spectrogram.
After each trap has been inspected, you can add images, comments, or audio notes about it. Not only is testing made easier with SONAPHONE and SteamExpert but so is paperwork. You can get fast reports at the end of the testing procedure, which can be viewed on your PC anytime.
All recorded data can also be revised and analyzed using the DataSuite web application.
The DataSuite SONAPHONE web application is used to manage the data collected using SONAPHONE. After SONAPHONE has collected all of the data, the web application can be used to evaluate it quickly and accurately.
The software provides us with all of the relevant measurement point information for all new and old devices. New traps can also be easily added to the software.
Being the leading engineering company in UAE, Technomax offers the primary source for Condition Monitoring of Steam Traps inspection for achieving improved reliability, with over 15 years of industry experience. To provide the best services, their dedicated, qualified, and experienced resources collaborate closely with customers. Technomax provides expert steam trap inspection and monitoring for better efficiency and increased lifespan.
Learn More About Our Services
Recent Blogs
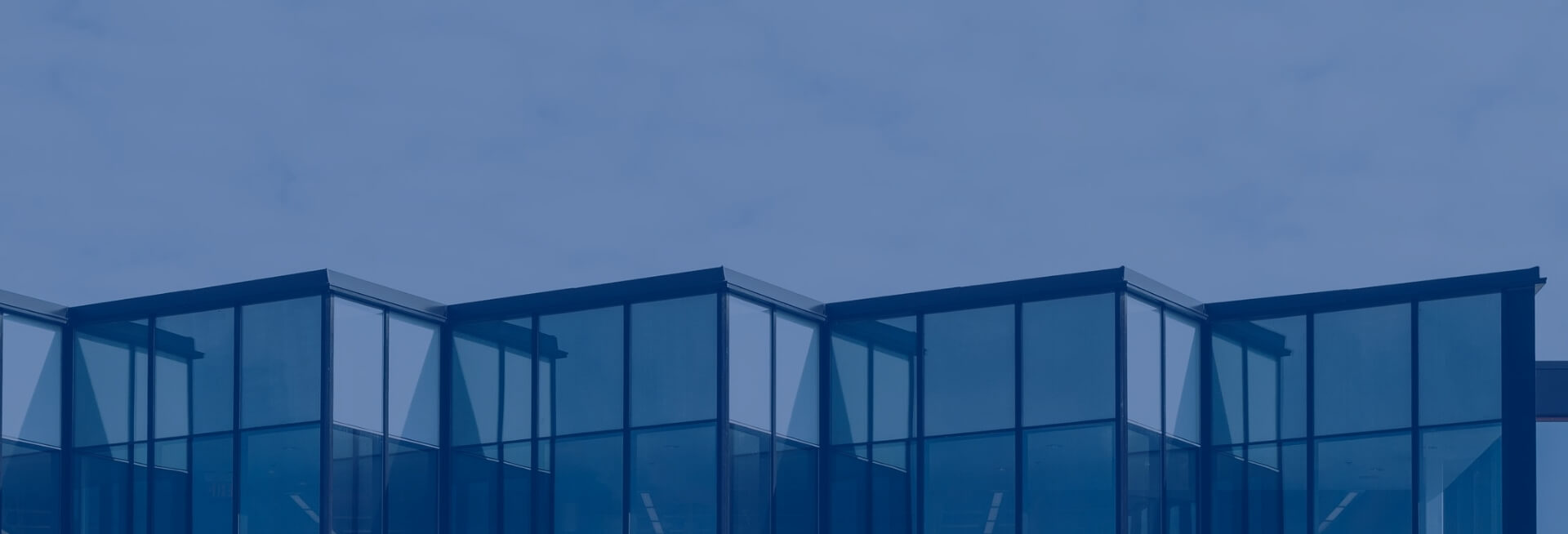
Get Started Now!
It takes less than a minute of your time. Or you may simply call +971 2 555 1 783