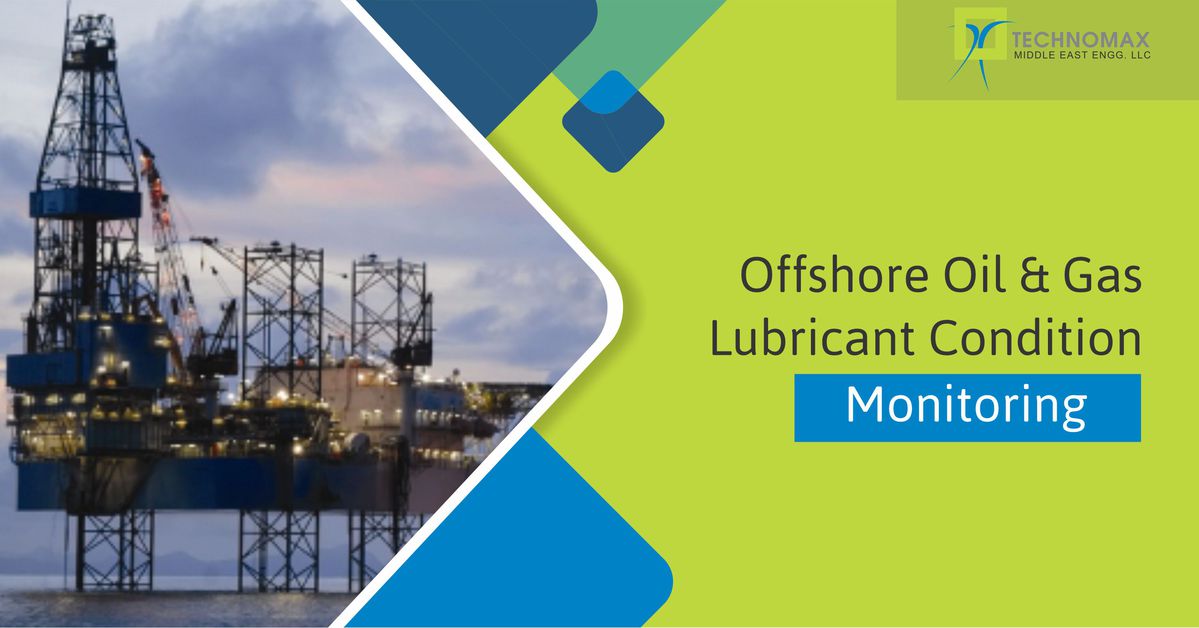
Introduction:
Onshore and offshore development projects in the oil and gas industry are predominantly capital-intensive investments, with the potential for severe financial and environmental consequences in the event of failure. Therefore, an efficient and effective maintenance management approach is essential to continuing production safely and reliably. This article explores the existing literature on condition monitoring development and its applications in the oil and gas industry. Read more about offshore oil and gas lubricants.
Condition monitoring in Oil and Gas:
Recent literature reinforces that the condition monitoring service's role is fundamental to the smooth, uninterrupted, efficient, and safe operation of oil and gas plants. The complex and integrated nature of oil and gas installations requires specific and carefully prepared condition monitoring programs with real-time condition monitoring data recording, analysis, and decision-making to accurately understand essential maintenance intervals. This, in turn, can promote the optimal use of plant equipment with higher levels of certainty and safety.
You may also like:
- What is Proactive Maintenance: Complete Guide
- Difference between preventive and predictive maintenance
- Detecting Misalignment Between IC Engines & Gas Compressors
Proactive Maintenance in Oil and Gas:
Proactive or preventive maintenance (PM) strategies are an essential component of an effective maintenance program. The PM strategy, known as condition-based maintenance or condition monitoring services, provides a dynamic understanding of the condition of the equipment during operation and is used to predict failures in mechanical systems, diagnosing failures of condition monitoring signals using diagnostics and prognoses.
Condition monitoring services strategies are currently at the center of maintenance and maintenance management research due to the trends and challenges mentioned above, the increasing complexity of industrial technologies, and advances in condition monitoring services that include the use of advanced digital online systems. Oil and gas projects are particularly large investments, with the potential for severe financial and environmental consequences in the event of a fatal failure.
Consequently, maintenance management is essential to continue production safely and reliably. According to one source, condition monitoring services are currently applied in the petrochemical industry, monitoring the condition of onshore and offshore oil and gas wells and generating additional production benefits in the 5% range.
Methodology:
The oil and gas industry mainly markets crude fossil fuels. Technomax focuses on optimizing energy consumption in oil and gas systems to increase revenues, address greenhouse gas emissions, and reduce operating costs, suggesting that "energy intensity trend" monitoring can guide maintenance management programs. This is because maintenance management directly impacts energy consumption and the optimization of oil and gas plants.
An advantage of an efficient condition monitoring service strategy here is that condition data reaches the people concerned, and maintenance activities can be concentrated where and when they are needed. Information and communication technologies (ICT) enable large companies to develop central maintenance centers that monitor remote facilities and notify and assist on-site maintenance personnel.
Remote structures are most often located at sea, in deep water. The significant challenges associated with inspecting offshore oil and gas production facilities in deep water underline the importance of permanent condition monitoring devices. Corrosion is a considerable concern at onshore and offshore oil and gas plants.
Failures in Oil and Gas Systems:
Oil refineries and gas treatment plants are large operations with many systems and subsystems operating simultaneously. Within and between each subsystem, there are separators, heat exchangers (condensers, boilers, and kettles), valves, purifiers, accumulators, piping systems, and rotating mechanical systems (induction motors, compressors, pumps, etc.). Each of these components can affect production, cause health and safety problems, and increase the environmental impact of operations in the event of a failure.
It is possible to have components on standby in some cases, but in other cases, the machinery or equipment is enormous, expensive, and complex; these machines and equipment are often the most suitable for condition monitoring services. Various processes take place between the incoming gas, the liquid raw material, and the final products.
Contact us for Laser shaft alignment
many different gas treatment configurations and does not include facilities that provide services such as steam, cooling water, and electricity. Plant project planning is complex, and the final solution is usually different. Common to most processes is the use of pumps, compressors, and heat exchangers. These intermediate components are used to control process parameters, such as flow rates, pressures, and temperatures. Technomax is the leader in providing condition monitoring services in Abu Dhabi.
Learn More About Our Services
Recent Blogs
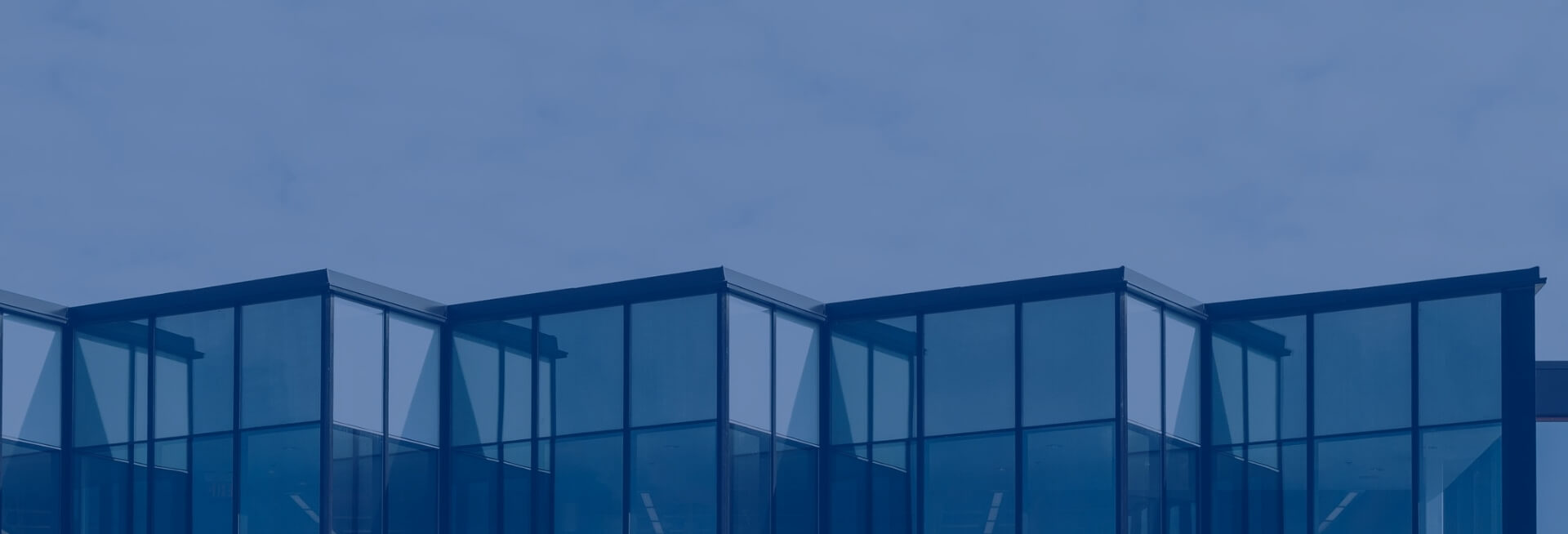
Get Started Now!
It takes less than a minute of your time. Or you may simply call +971 2 555 1 783